Case Study
Cargill Turkey Products
Overview
Cargill Turkey Products processes 7.4 million pounds of product per week. The 330,000-square-foot plant is home to 1,200 employees. Competition in the industry is high, making it challenging to pass cost increases on to consumers. With volatile commodity markets, the price of feed was increasing, driving up the cost of turkeys. Rising utility rates have put additional pressure on prices.
Electricity is a major line item for the plant at more than $2 million per year for two large electric accounts. They were challenged to find cost-saving opportunities and decided to focus on reducing their utility bills turning to the experts at UMS.
Based on the specific needs and usage patterns of the plant, the analysts were able to identify lower pricing options and contract terms for the plant. They negotiated and executed a much more favorable Power Purchase agreement with the power provider.
Collectively, the plant is saving $197,000 per year as a result of this work. This has improved the bottom line for the plant and earned accolades and recognition from management for Karen (pictured left) for initiating this project.
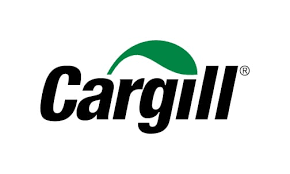
The Facts
- Cargill Turkey Plant processes 7.4 million pounds of product per week
- With the cost of feed rising and them being in a competitive market, they were looking for ways to reduce costs
- After receiving a recent copy of each of their facility's bills analysts got to work
- Once the analysis was complete over $197,000 in annual savings were found